FLOW-3D is a CFD software package developed by Flow Science, Inc. FLOW-3D is a powerful computational fluid dynamics tool that specializes in simulating free-surface flows, particularly in applications such as casting, metal forming, microfluidics, and other scenarios where fluid-solid interaction is crucial.
Key features of FLOW-3D may include:
- Free-Surface Flow Simulation: It excels in simulating complex free-surface flows where the interaction between fluid and solid boundaries is significant.
- Multiphysics Simulations: FLOW-3D often supports multiphysics simulations, allowing users to model phenomena such as heat transfer, solidification, and fluid-structure interaction.
- User-Friendly Interface: It typically provides a user-friendly interface for setting up simulations, defining boundary conditions, and analyzing results.
- Meshing Capabilities: The software offers tools for mesh generation to discretize the computational domain.
- Post-Processing Tools: FLOW-3D includes tools for visualizing and analyzing simulation results, aiding users in understanding the behavior of the simulated flow.
What’s New in FLOW-3D 2023R2
New results file format
We introduced an all-new results file format based on the EXODUS II format, enabling faster postprocessing in FLOW-3D and FLOW-3D POST 2023R2. This new file format significantly reduces the time spent on postprocessing tasks for large, complex simulations (up to 5x on average!) while improving connectivity with other visualization tools. Users now have the choice to write Selected data in either flsgrf, EXODUS II, or both flsgrf and EXODUS II file formats. The new EXODUS II file format utilizes finite element meshes for each object, which allows users to also open FLOW-3D results with other compatible postprocessors and FEA codes. With the new workflow, users can visualize large, complex cases quickly and extract auxiliary information using arbitrary slicing, volume renders, and statistics.
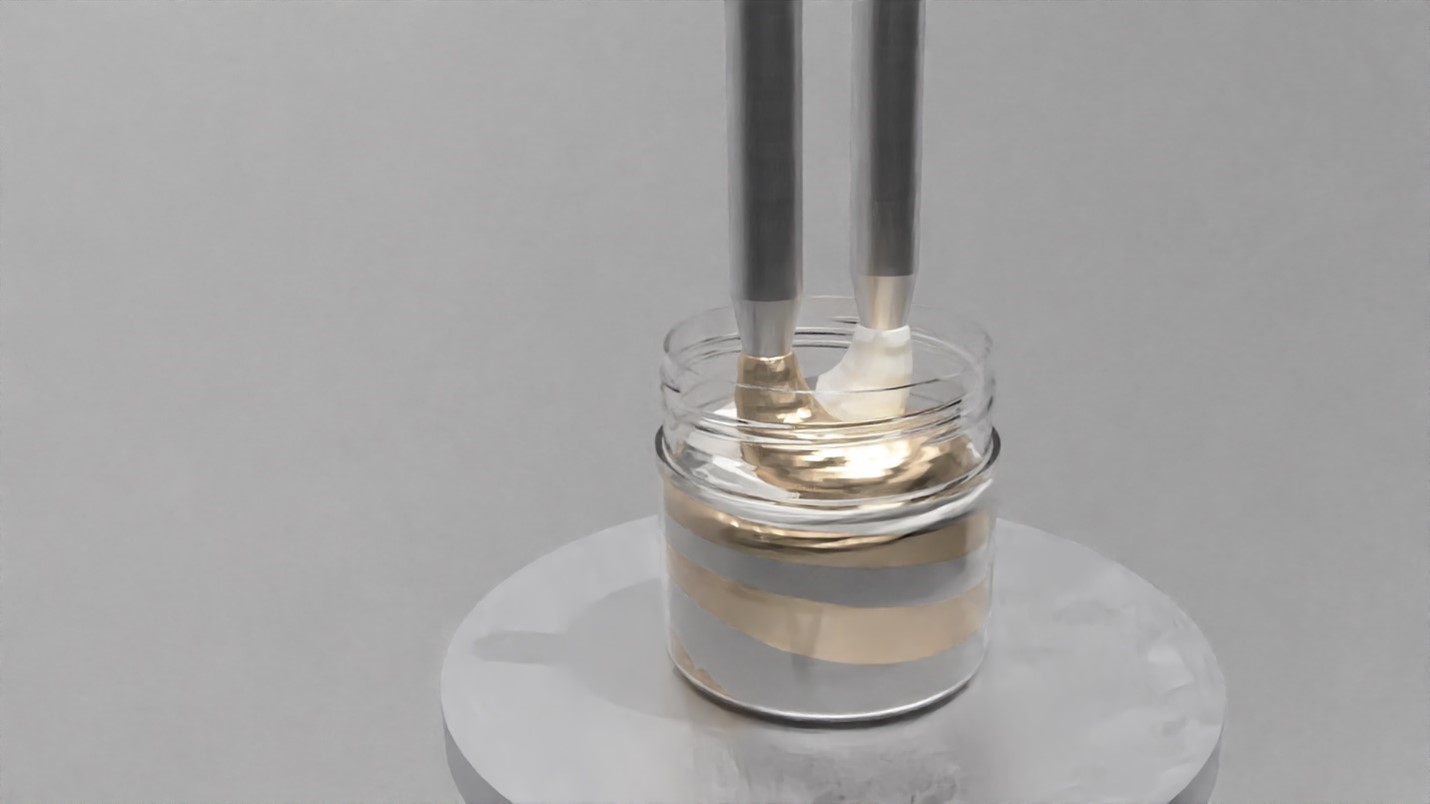
The new results file format boasts a remarkable speed-up in visualization workflows compared to flsgrf without sacrificing the performance of the solver engine. This exciting new development provides a seamless simulation experience with improved speed and flexibility in results analysis. Learn more about the new visualization capabilities in FLOW-3D POST.
Turbulence model improvements
FLOW-3D 2023R2 brings a major improvement to the dynamic mixing length calculation for two-equation (RANS) turbulence models. In certain limiting cases such as near-laminar flow regimes, the code-computed limiter could in previous versions sometimes be overpredicted, forcing the user to manually input a specific mixing length. The new dynamic mixing length calculation better accounts for the turbulent length and time scales in these situations. Users can now apply the dynamic model to a wider range of flows, instead of setting a fixed (physics-based) mixing length.
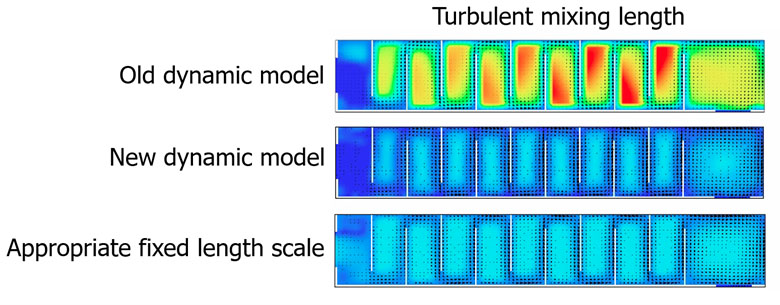
Hydrostatic pressure initialization
It is often necessary for users to initialize hydrostatic pressure in pre-defined fluid regions. Previously in large, complex simulations, the hydrostatic pressure solver could sometimes be slow to converge. FLOW-3D 2023R2 brings a significant performance improvement to the hydrostatic solver, enabling it to converge up to ~6x faster during the preprocessing stage.
Compressible flow solver performance
FLOW-3D 2023R2 introduces an optimized pressure solver, giving significant performance gains for compressible flow problems. In this example of a compressible jet flow, the 2023R2 solver was ~4x faster than the 2023R1 version.
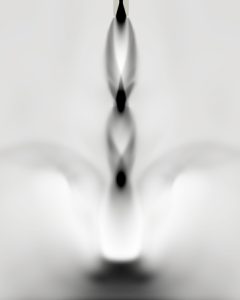
What’s New in FLOW-3D 2023R1
All products in the FLOW-3D software family received IT-related improvements in 2023R1. FLOW-3D 2023R1 now supports Windows 11 and RHEL 8. Our Linux installer has been improved to report missing dependencies and it no longer requires root-level permissions, which makes installation easier and more secure. And for those of you who have automated your workflows, we added a command-line interface to our input file converter so that you can ensure your workflow is working with updated input files, even in scripted environments.
Expanded PQ2 analysis
Hydraulic systems used in manufacturing can be modeled using PQ2 curves. It is often a convenient simplification to approximate the hydraulic system using a mass-momentum source or a velocity boundary condition to skip the details of the device and include its impact on the flow. We expanded our existing PQ2 analysis model to allow for this type of geometric simplification while still giving realistic results. This translates to a reduction in simulation time and model complexity.
https://youtube.com/watch?v=u9WJGPlNy8s%3Fcontrols%3D1%26rel%3D0%26playsinline%3D0%26modestbranding%3D0%26autoplay%3D0%26enablejsapi%3D1%26origin%3Dhttps%253A%252F%252Fwww.flow3d.com%26widgetid%3D1
What’s New in FLOW-3D 2022R2
With the release of the FLOW-3D 2022R2 product family, Flow Science has unified the workstation and HPC versions of FLOW-3D to deliver a single solver engine capable of taking advantage of any type of hardware architecture, from single node CPU configurations to multi-node parallel high performance computing executions. Additional developments include a new log conformation tensor method for visco-elastic flows, continued solver speed performance improvements, advanced cooling channel and phantom component controls, and improved entrained air functionalities.
Unified solver
We migrated our FLOW-3D products to a single, unified solver to run seamlessly on local workstations or on high performance computing hardware environments.
Many users run their models on laptops or local workstations, but in addition run larger models on high performance computing clusters. With the 2022R2 release, the unified solver allows users to exploit the same benefits of OpenMP/MPI hybrid parallelization from HPC solutions to run on workstations and laptops.
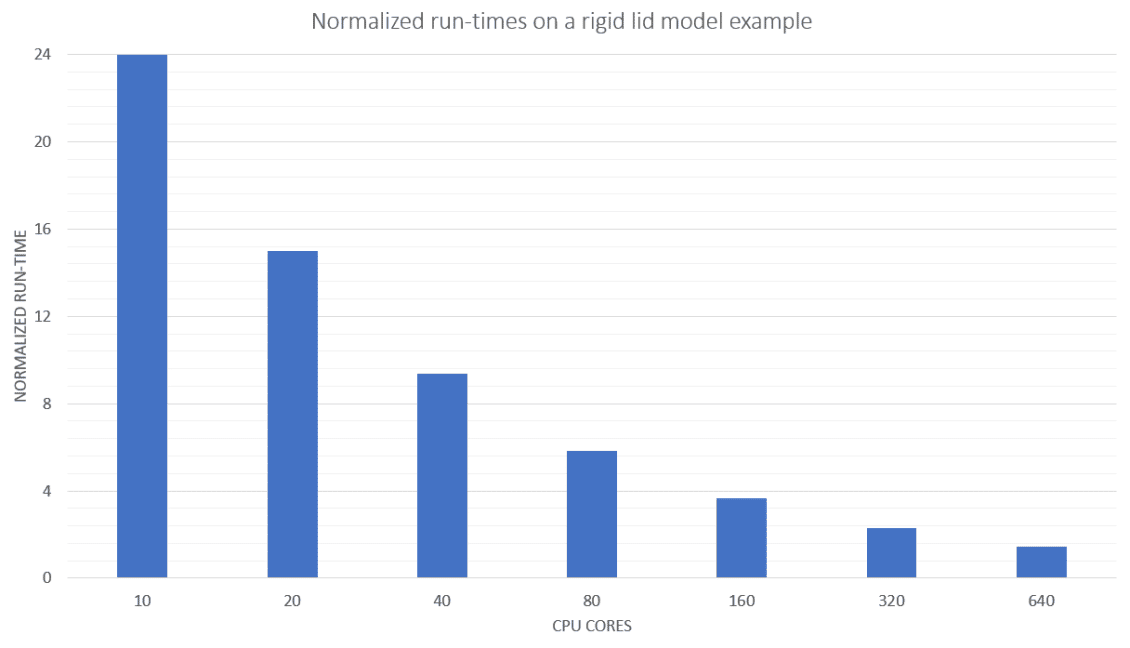
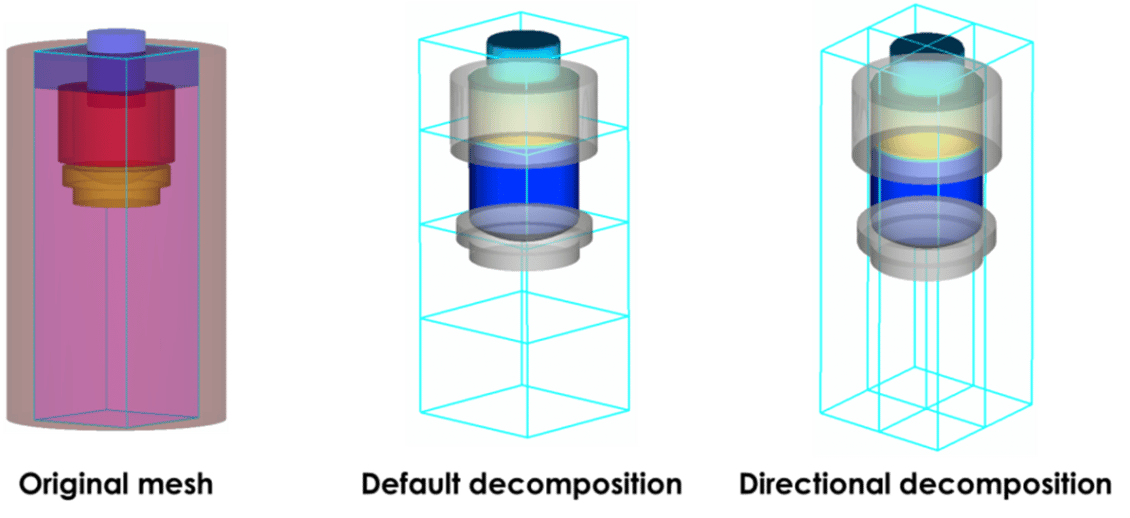
Solver performance improvements
Multi socket workstations
Multi socket workstations are now very common and capable of running large simulations. With the new unified solver, users using this type of hardware will generally see performance gains from being able to run models taking advantage of OpenMP/MPI hybrid parallelization that used to be only available on HPC cluster configurations.
Low level routines improved vectorization and memory access
Performance gains on the order of 10% to 20% have been observed for most test cases, with some cases yielding run-time benefits in excess of 20%.
Refined volumetric convective stability limit
Time step stability limit is a major driver in model runtime, with 2022R2, a new time step stability limit, 3D convective stability limit, is available in the numerics widget. For models that are running and convection limited (cx, cy, or cz limits) the new option has shown typical speed-ups on the order of 30%.
Pressure solver pre-conditioner
In some cases, for challenging flow configurations, run times can be drawn out due to excessive pressure solver iterations. For those difficult cases, with 2022R2, when a model iterates too heavily, FLOW-3D automatically activates a new pre-conditioner to help with pressure convergence. Tests have improvements in runtime anywhere from 1.9 to 335x faster!
Log conformation tensor method for visco-elastic fluids
A new solver option for visco-elastic fluids is available to our users, and is particularly effective for high Weissenberg numbers.
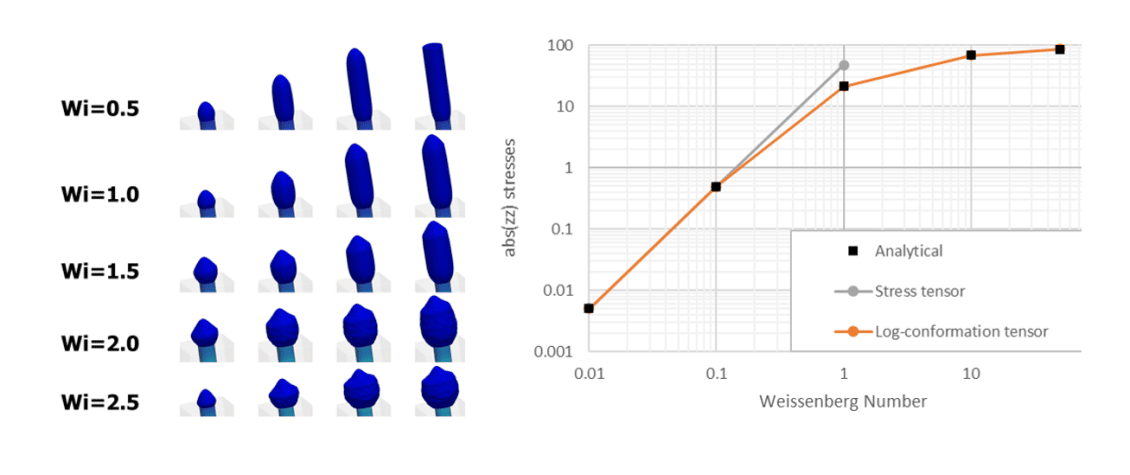
Active simulation control extensions
Active simulation control functionalities have been extended to include phantom objects, commonly used for continuous casting and additive manufacturing applications, as well as for cooling channels, used in casting and in many other thermal management applications.
Improved entrained air functionalities
For diffusers and similar industrial bubble flow applications, mass sources can now be used to introduce air into the water column. In addition, default values for the turbulent diffusion of entrained air and dissolved oxygen have been updated, and model accuracy for very low air concentrations has been improved.
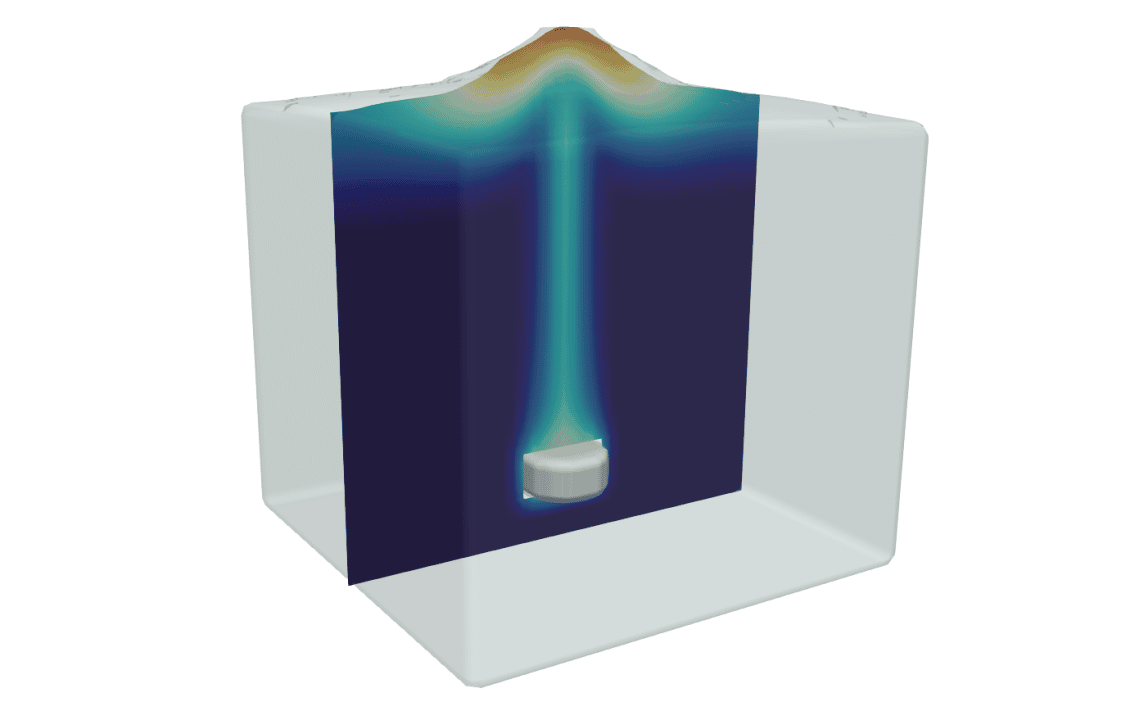