Additive manufacturing and software tools facilitate heat exchanger design, resulting in improved performance in many thermal management applications.With product design becoming increasingly complex in nearly every industry, engineers have to do more with less, especially when it comes to thermal management. Appropriately managing product temperature is a difficult task with multiple design constraints.
nTopology has submitted this post. Written by: nTopology
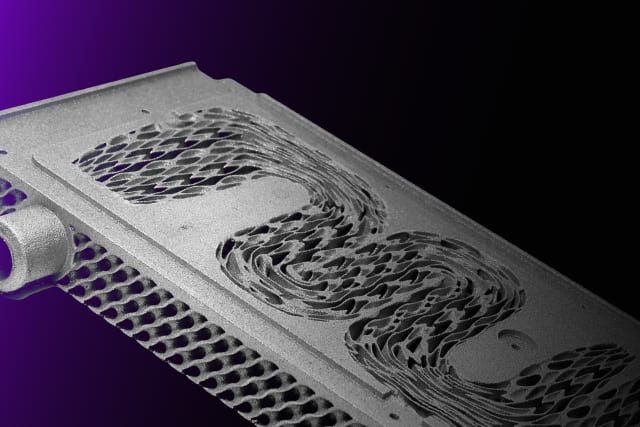
(Image courtesy of nTopology.)
With product design becoming increasingly complex in nearly every industry, engineers have to do more with less, especially when it comes to thermal management. Appropriately managing product temperature is a difficult task with multiple design constraints.
For decades, engineers have done their best to work around these constraints, but they are limited by manufacturing technology. Advances in software tools such as computational fluid dynamics (CFD) and in manufacturing processes such as 3D printing can help manufacturers develop innovative heat exchanger (HEX) designs.
Engineers can continue to discuss the benefits of additive manufacturing (AM), but organizations need to see tangible results to invest in the technology. Seeing first-hand how additive manufacturing and software tools can address traditional thermal management problems can help create buy-in. Below are a few applications where additive manufacturing and software design improved thermal management.
1. Fuel-Cooled Oil Coolers
Heat exchangers cool the engine and gearbox oil in many industrial processing or power generation rigs. These same heat exchangers also preheat cold fuel to improve combustion efficiency.
Engineers face size and weight constraints as off-the-shelf shell and tube oil coolers are too large or heavy for miniaturized or mobile systems. To address these constraints, engineers can look to develop new heat exchanger designs that keep the heat transfer area constant while reducing size and mass.
In one example, the nTopology team accomplished this by designing a heat exchanger with a gyroid lattice core. Engineers used nTopology for effective design generation and developed new geometry that was 80 percent lighter than the old one. The design had a 1.8x higher heat transfer coefficient and passed ASTM quality standards.
2. Conformal Cooling
In aerospace applications, weight is one of the top design priorities. Auxiliary power units (APU) are turbine generators that crank out massive amounts of power in small packages. These units are vital in various aerospace applications, and design teams are always looking to reduce the weight of these devices.
Thermal management is one of the main constraints of APUs. The KW Micro Power team was able to design around this constraint as they looked to redesign the casing of their APU. Engineers were able to take advantage of additive manufacturing and nTopology’s advanced software to develop an entirely new casing design. To accomplish this, the team created a multifunctional microturbine housing with embedded cooling channels.
Their team achieved this by applying a shell with variable thickness to their generator’s housing and removing material from areas not bearing significant loads. Overall, the team reduced the generator’s weight by 44 percent while simultaneously reducing the operating temperature by 33 percent
3. Electronics Cooling
In the race to electrification, thermal management is more critical than ever. Engineers must effectively cool electronic components to maintain product reliability. Cold plates are an effective solution for the thermal management of electronic devices. However, one persistent issue is the heat exchanger’s size which limits thermal performance. To address this limitation, engineers can take advantage of additive manufacturing.
A simulation-driven approach can be used to optimize the heat exchanger’s lattice core design. Computational fluid dynamics and thermal analysis help designers identify the correct flow paths through the corresponding channels. This optimization improves the heat transfer coefficient without increasing the overall size of the heat exchanger.
4. Heat Sinks
Forced convection heat sinks are another application where additive manufacturing is effectively utilized. Developing unique structures that take advantage of lattice surfaces improves multiple heat sink characteristics. Additive manufacturing allows these heat sinks to be optimized for thickness and cell size to promote conduction while maximizing airflow.
Using beam-based lattice structures increases surface area and helps improve turbulent flow. Reusable workflows also allow designers to develop iterative models without starting the design process from scratch. Teams can reduce design process time and get to market faster.
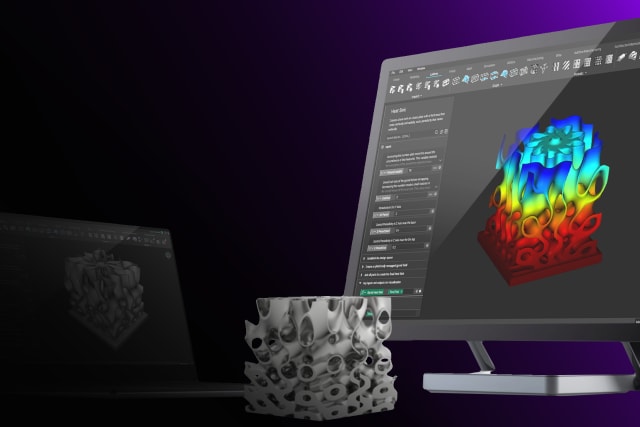
(Image courtesy of nTopology.)
5. Semiconductor Wafer Table
The semiconductor manufacturing industry was one of the supply chains hit the hardest during the pandemic. As a result, semiconductor manufacturers are under more pressure than ever before to upgrade their production capacity. This means that semiconductor design engineers must develop increasingly innovative designs.
During lithography, engineers have to keep temperatures within tight ranges, or semiconductor quality can be compromised. Engineers use wafer tables for thermal tempering during the fabrication process. If there are any issues with wafer table quality, semiconductor manufacturers will be unable to ensure manufacturing accuracy.
Engineers can utilize AM to design and manufacture for specific thermal loads. Using a sample temperature field, engineers can identify the optimal geometry location and orientation of the wafer cooling disc. Engineers are able to further alter designs to ensure proper thermal management for heat dissipation and the reduction of disc distortion.
6. Flow Guides
Ensuring proper fluid flow through pipes and manifolds by utilizing heat exchangers is a difficult task. Engineers use flow guides to eliminate dead zones in pipes and manifolds while reducing pressure drops. However, determining the proper fin design for heat exchangers can be better accomplished through simulation and additive manufacturing.
Engineers can utilize computational fluid dynamics data to optimize heat exchanger designs. This data ensures that HEX geometry will alter the fluid flow to generate the least resistant flow path—minimizing energy loss. Engineers can easily manipulate fin sizing, spacing and thickness to find the best design for their applications.
7. Air Ducts
A network of air ducts enables airflow to heat and cool everything from houses to cars. Regardless of the end application, minimizing energy loss through air duct systems is paramount to building energy-efficient HVAC systems. Additive manufacturing enables manufacturers to consolidate air duct assemblies into a single component.
Engineers can use multiple methods to achieve improved air duct performance. Fluid dynamics software enables engineers to optimize duct airflow, resulting in more effective heating and cooling. For example, adding a dimpling pattern —via additive manufacturing—to an air inlet creates local eddy currents near the channel walls, reducing drag and increasing flow intake.
8. Hydraulic Manifolds and Nozzles
Hydraulic manifolds and nozzles regulate fluid flow to produce kinetic energy. Engineers can utilize additive manufacturing to design manifolds and nozzles optimized for weight and flow characteristics. Manufacturers can create designs that improve flow uniformity or reduce pressure drops.
Manufacturers utilize AM to create gyroid lattice structure cores to improve performance at a more compact size. These cores can hinder fluid flow, but engineers can design around this constraint with CFD simulation. This simulation allows engineers to improve flow uniformity in outlets and heat exchanger cores.
Engineers can utilize computational fluid dynamics data at the start of the design process. Instead of wasting precious time and resources on remaking old designs, engineers can then use an iterative workflow to develop better designs.
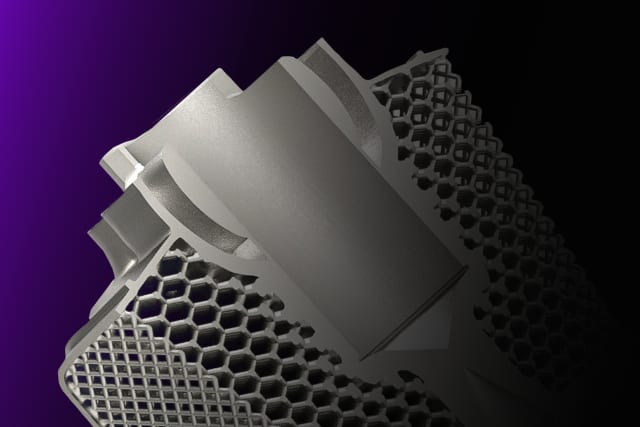
(Image courtesy of nTopology.)
nTopology Helps Engineers Optimize Thermal Performance
The future is bright for additive manufacturing and thermal management applications. There are many real-world examples and applications where AM and nTopology can make a significant difference in thermal performance.
The examples above showcase how manufacturers can drive significant efficiency gains and create more reliable products using AM and next-generation engineering design software like nTopology.
Are you interested in learning more about nTopology software and how to improve thermal performance in your application? Download our Thermal Management Guide here.