Simcenter 3D 2206 and Symphony Pro bring changes on both big and small scales.Simcenter 3D is Siemens Digital Industries Software’s comprehensive multidisciplinary simulation flagship. Simcenter 3D 2206 was released recently with several new features and smaller quality-of-life improvements.
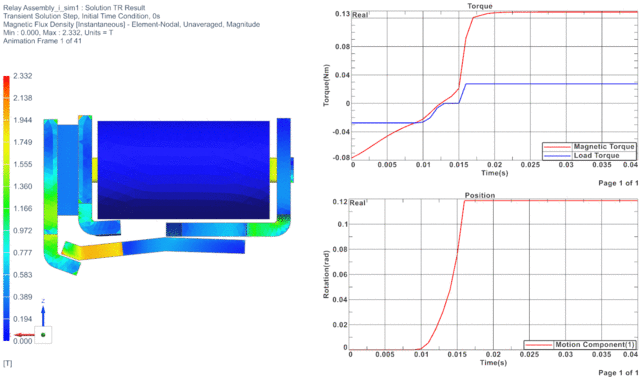
Electromagnetic simulation visualizes torque over time. (Image courtesy of Siemens.)
On the chip side of manufacturing, the new Symphony Pro platform offers electronics simulation. The tool seeks to be a standout in the electronics simulation landscape, focusing on speed and the fidelity of results. The Symphony Pro offering, which is a complement to Simcenter 3D, shows how the company can help engineers design integrated circuits required for electronics while also designing the systems where those electronics will reside.
Product design and development isn’t going to slow down anytime soon, and simulation engineers are going to need tools that can adapt to the changing needs of society. Supply chain issues, inflation and whatever global challenge is next on the horizon are going to keep the requirements of manufacturing fluid and unpredictable. Simcenter 3D is demonstrating a commitment to adding features and adapting to the shifting manufacturing landscape.
Aircraft Design, Fatigue and Fluid Dynamics
Feature additions are the big news for Simcenter 3D 2206. Simulation engineers get enhancements for aircraft studies, structure analysis, and computational fluid dynamics (CFD). Building a global finite element modeling (GFEM) system for an aircraft is a substantial task, but collecting and distributing the results can be just as difficult. Some companies have engineers focus on building code to format results from several studies. However, their time would be better spent running stress analysis.
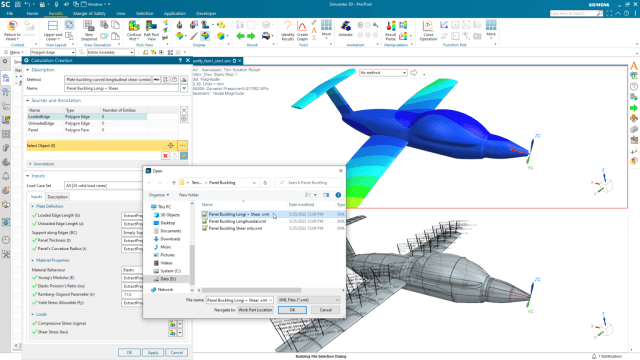
More efficient simulation modeling produces faster results. (Image courtesy of Siemens.)
Simcenter 3D already had a margin of safety tool built into the software to understand changes in the geometry or the material of a structure and how the results could be affected. Now the tool will react to model changes by automatically updating the geometry in the study, creating a new mesh and updating the results. This is a huge time-saver. The other big benefit to aircraft structural studies is the Calculation Template, which provides a set of base conditions from which an aircraft design team can run studies, ensuring that every study uses the same extracted loads.
A company as big as Siemens has products to meet a range of needs, and the 2206 revision adds some new ties between Simcenter 3D and STAR-CCM+. Linking computational fluid dynamics (CFD) and finite element analysis is a boon for mobility engineers, as it models the effects of watercraft or airflow. A recent blog shows two benefits to having the CFD and structure studies originate from the same software family. First, Simcenter 3D gets the fluid pressure data directly from the CFD mesh—at every time step in the process. Second, the data file only needs to be imported into Simcenter 3D once. This means that changes in the structural design of a watercraft can be run right away without fussing with boundary conditions or mesh considerations.
Fatigue analysis is another area feeling the boost from the 2206 release, with the addition of new features. The Block Load Event can set up load cases to act as a foundation for studies based on a company’s best practices. Now different materials can be studied against different load cases, all using the same base to shorten the overall time spent on a project. This setup works not just for different load magnitudes but also for different loading methods. Torsion, bending or tension loads are added to the same event interface.
Symphony Pro and Mixed-Signal Analysis
Mixed-signal analysis requires engineers who have a wide array of skill sets. There are analog requirements mixed right in with the digital requirements. Pressure, temperature, light levels, sound levels and vibration are all inputs from the physical world that need to be transformed into digital signals. This isn’t new, but the amount of physical data is growing, the space allowed for processing it is shrinking, and the time spent running these analyses needs to be faster.
Electronics must be portable and with those requirements come new constraints. Power consumption is tightly managed to make the system last longer on a single charge. Different parts of the system can power down when they are not directly in use. This requires designers to isolate the different blocks of a system so that one part powering down does not affect neighboring blocks, and there is some state retention necessary so that powering a system back up doesn’t require a new load.
Symphony Pro uses real number modeling (RNM) to analyze mixed-signal systems. A feedback loop of building the model, verifying the model, and using the model improves the quality of a study. The main advantage here is that the testing phases are moved up in the design process. Being able to run simulations at the early design phases saves time and ideally will identify unintended issues before they become disruptions.
What Does It All Mean?
System on a chip (SoC) applications are huge, and society’s need for sophisticated electronic functions on all levels of a product is only going to grow. Ten years ago, we could all envision a smartphone. But what about a multifunctional dog collar or a smart teakettle? The Internet of Things (IoT) quickly turned up the adoption level and now everything needs chips—and all of those chips need designs.
Siemens Symphony Pro is positioned to give electronics engineers a great tool for designing these smart applications. Making incrementally smarter decisions earlier in the design cycle gives companies a technical advantage over their competitors. Symphony Pro will also work with the Siemens EDA Questa logic simulator, giving users an accelerated method of electronic design automation (EDA).
While Symphony Pro works on small-scale electronics problems, Simcenter 3D 2206 is ready to help users on their larger projects. The features added in this new revision can immediately help aircraft and watercraft engineers. Strength and fatigue engineers who take the time to build the load events into studies can also save time and get better results.
Simcenter 3D is tasked with doing many things for many stakeholders. But with each release, the user base is the most important focus as fixing bugs and responding to quality-of-life requests provides immediate satisfaction. NVH prediction, wire harness design, flexible pipe and small duct acoustics all see enhancements in this new revision. In the larger Siemens environment, Simcenter 3D also needs to interface with other company tools, and the benefits to these interactions is huge when something like FEM and CFD can come together. Mixed in with these concerns is future planning. What will simulation engineers need in five or 10 years? It’s incredibly difficult to answer this question, but companies need to work on these forward-facing requirements before they even exist.